
Understanding Air-Covered Yarn
Air-covered yarn is a distinctive type of composite yarn that integrates multiple fibers using an air jet process. Composed primarily of a core thread wrapped by another filament through high-pressure air, these yarns achieve a balanced combination of properties from both materials involved.
The production process starts with selecting raw materials such as nylon, polyester, or spandex for both the core and covering filaments. The primary stages include feeding the fibers into an air texturizer where they are entangled and intertwined under controlled tension and pressure settings. Key benefits of this approach involve enhanced elasticity, improved uniformity, and tailored texture—making air-covered yarn suitable for diverse applications spanning fashion garments to technical textiles.
Key Customization Parameters
Fiber Selection
The choice of fibers dramatically influences the properties of air-covered yarn. Natural fibers like cotton provide softness and breathability, while synthetic fibers like polyester and nylon offer strength and durability. By blending different types of fibers, manufacturers can create yarns with specific characteristics suited to particular uses—for instance, combining polyester with spandex enhances both stretchability and resilience.
Yarn Count and Denier
Yarn count and denier refer to the thickness and weight of the yarn, crucial factors determining its suitability for various applications. A higher denier indicates a thicker yarn, ideal for heavy-duty fabrics, whereas a lower denier is suitable for softer, delicate textiles. Tailoring the yarn count ensures optimal performance whether it be for robust sportswear or elegant evening gowns.
Twist and Texturing
Adjusting the twist level of yarn affects its strength and flexibility. More twists per inch increase tenacity but may reduce softness. Additionally, texturing techniques, which modify the surface structure of the yarn, enhance thermal insulation, moisture-wicking capacity, and tactile comfort—a paramount consideration for functional and comfortable clothing.
Customization Techniques
Air-Jet Texturing
Air-jet texturing involves blasting continuous filaments with high-pressure air to create bulked yarns. This method imparts natural-like textures without sacrificing tensile strength, benefiting applications requiring nuanced aesthetics combined with robust performance. For example, textiles used in fashion apparel and home furnishings often employ air-jet textured yarn for added plushness and visual appeal.
Mechanical Crimping
Mechanical crimping introduces wavy contours along the yarn’s length via deformation techniques. It results in voluminous yet lightweight fabrics, perfect for activewear that demands freedom of movement alongside adequate support. These crimp-induced properties ensure products retain shape integrity after extensive use or repeated laundering.
Heat Setting
Heat setting stabilizes the configurations achieved during crimping and other processes by applying precise thermal treatments. Ensuring dimensional stability and reducing shrinkage, heat-set yarns are integral to industries prioritizing longevity and consistent fabric performance, such as automotive textiles.
Application-Specific Customization
Apparel and Fashion Industry
In fashion, customization focuses on balancing aesthetic requirements with wearing comfort. Clothing must not only look appealing but also withstand usage strains. Air-covered yarns customized for fashion can meet these needs with ease by offering stretch, drape, and resistance to wear and tear.
Medical Textiles
Sterilization compatibility and biocompatibility define medical textile applications. Fibers are chosen to ensure they can endure sterilization processes without degrading while remaining safe for prolonged contact with human tissue. Customized air-covered yarns in this sector often focus on hygiene and non-reactivity.
Automotive Textiles
Fire retardancy and abrasion resistance are pivotal for automotive textiles. Yarns designed for vehicle interiors must comply with stringent safety standards, necessitating custom blends that resist ignition and wear while maintaining aesthetic and functional strengths.
Technical and Industrial Textiles
High-performance attributes and environmental considerations dominate technical textiles. Customized solutions for industrial purposes might feature heightened durability against mechanical stresses or optimized longevity even in extreme conditions, supported by eco-friendly material choices.
Case Studies and Real-World Examples
Success Story in Sportswear Manufacturing
A notable example involves a sportswear brand that leverages air-covered yarn customized for moisture-wicking, stretch, and recovery properties. The resultant athletic gear performs reliably across arduous physical activities while ensuring wearer comfort.
Innovations in Protective Gear
Protective equipment manufacturers have adopted high-tenacity fibers within air-covered yarns for impact-resistant textiles utilized in protective uniforms. These enhancements significantly elevate user safety in hazardous scenarios.
Advancements in Smart Textiles
Smart textiles incorporating electronic components benefit immensely from fine-tuned air-covered yarns that facilitate sensor embedding without compromising fabric consistency. Innovations pave the way for sophisticated wearable technology integrating functionality with traditional textile comfort.
Future Trends and Innovations
Sustainable Customization Practices
With increasing environmental awareness, the textile industry is inclining towards sustainable practices. Eco-friendly materials and energy-efficient manufacturing methods guide future developments in customizable air-covered yarns.
Technological Advancements
Automation and artificial intelligence are revolutionizing customization, enabling precision in creating yarns tailored explicitly to customer specs while enhancing operational efficiency and minimizing waste.
Emerging Markets and Opportunities
Expanding markets in wearable tech and recyclable textiles indicate growing demand for specialized air-covered yarn products. Flexibility in adapting to evolving market trends positions manufacturers strategically for tapping into these lucrative opportunities.
Practical Tips for Manufacturers
Collaboration with Suppliers and Designers
Clear communication between suppliers, designers, and manufacturers is vital. Partnerships foster joint development projects focused on innovative textile solutions achieving mutual objectives.
Quality Control and Testing
Consistency in product quality assures users dependability. Implementing rigorous testing protocols validates performance specifications, reinforcing reliability in customized yarn offerings.
Market Analysis and Customer Feedback
Adaptive strategies grounded in thorough market analysis and responsive customer feedback loops drive progressive refinement in yarn customization, aligning products closely with consumer expectations.
Final Thoughts
Customization unveils expansive potentials for air-covered yarn, marrying practical utility with design versatility. Encouraging continual innovation, today’s developments spell exciting prospects for tomorrow’s textiles. Explore the transformative advantages achievable through bespoke yarn integration.
Additional Resources
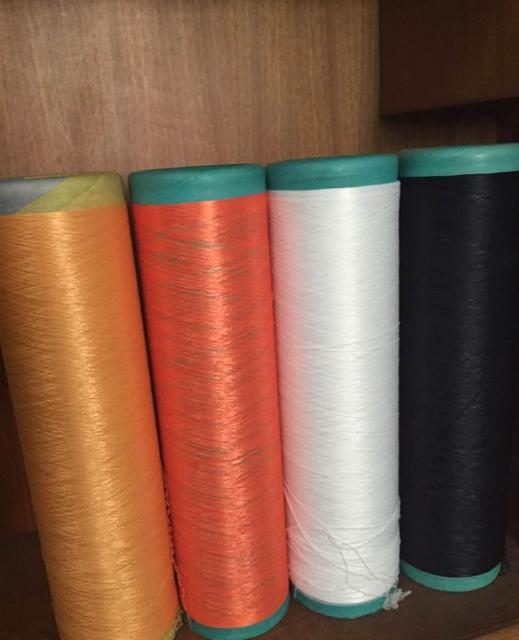